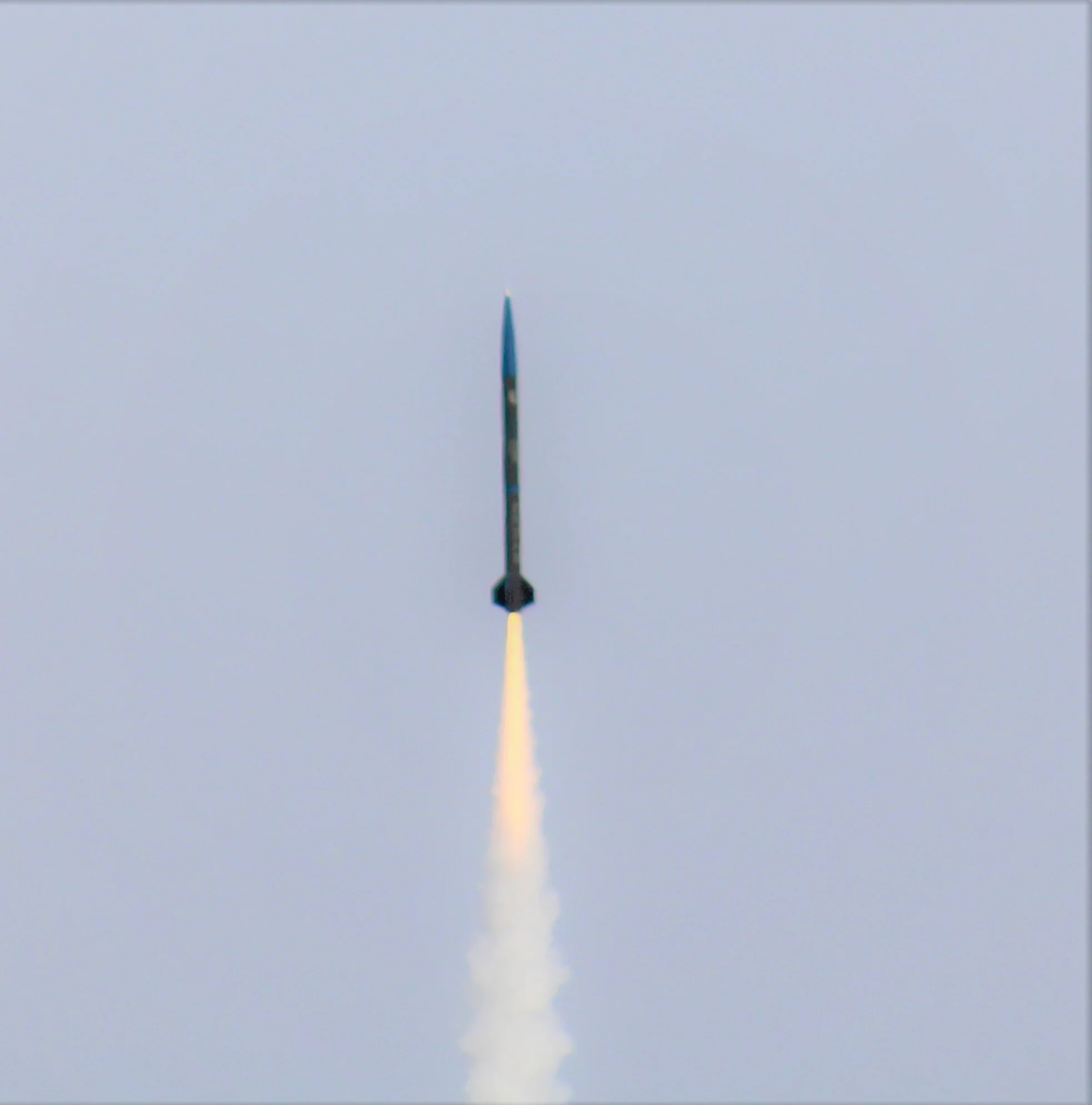
PAST LAUNCH VEHICLE PROJECTS
Ticonderoga
Designed and constructed in the Fall of 2018, Ticonderoga was the prototype rocket for Noctua II. The purpose of Ticonderoga was to learn and develop the team’s ability to construct minimum diameter carbon fiber airframes. A minimum diameter vehicle implies that the body tubes are as small as the motor will allow. This design vastly reduces drag, resulting in a much more efficient rocket. Eclipse plans on launching a rocket to 30,000 ft on a custom hybrid rocket engine, and in order to achieve such an altitude, a minimum diameter vehicle is essential. The biggest challenge with such a design is securely attaching fins to the rocket. Ticonderoga was successfully launched and recovered, validating the team’s process of creating a minimum diameter launch vehicle.
Epoxyless Project - "Firebolt"
Epoxy is a chemical binder similar to glue, which after drying, creates a strong chemical bond between two components. Due to its ease of use, strength, and wide array of effective application surfaces, epoxy has become a very popular binder for high powered rocketry as well as other building projects.
The goal for the Epoxyless Project was to design, build and launch a rocket without the use of any epoxy or glue. An intriguing engineering challenge, finding ways to connect components without adhesives is also useful for the future of Rice Eclipse in situations where using glue is not enough as we work towards our goal of building higher power rockets that reach earth’s atmosphere. With this in mind, Firebolt was born.
Instead of epoxy, Firebolt uses nylon bolts to connect all of its components and is a modified version of our level 1 certificate rockets. Several 3D printed parts were designed and manufactured at the OEDK such as fin brackets to hold the fins in place and motor centering rings which hold the motor inside the body of the rocket.
3D printed fin bracket used on the epoxyless rocket
Firebolt’s first launch was 4/19/17 under an -135 aerojet motor. While successful under powered flight, Firebolt became unstable after the motor stopped firing and tumbled out of the air. Fortunately it was recovered safely and will be relaunched in the future with larger fins which was where we determined the point of failure was with the help of our Tripoli advisors.
SEDS Competition - "Snoopy"
Phil ('19) and Jeff ('20) setting up Snoopy for it's first launch
This is a two-stage, dual-deploy, scratch-built rocket that Eclipse will enter into the SEDS University Student Rocketry Competition. Our entry is based on the club’s original L1 certificate rocket design, modified to include two distinct stages: a booster stage, and a sustainer stage. The booster stage is powered by a single I-class commercial solid-fueled ammonium perchlorate composite propellant motor, and also contains its own recovery system (a 40” parachute). The sustainer stage is comprised of two body tubes attached by a coupler. The lower tube contains the sustainer’s H-class commercial solid-fueled ammonium perchlorate composite propellant motor, and also houses the sustainer’s drogue parachute (a 12” nylon parachute) at the top of the lower tube. The coupler contains the rocket’s avionics bay, including the competition altimeter, the stage timer for igniting the sustainer, and a second altimeter to trigger the dual-deployment recovery system. The coupler is glued to the upper tube and is friction-fit to the lower tube, so the avionics bay remains attached to the upper tube after the drogue chute is deployed. This allows the secondary altimeter to also trigger the sustainer’s main parachute (a 60” nylon parachute) at a specified altitude, which is housed in the sustainer’s upper tube (and is deployed out the top after ejecting the nose cone).
The purpose of this rocket is to get practical design experience with avionics-triggered, multiple-deploy recovery systems. Such systems will be valuable to future Eclipse designs, so this rocket will serve as a first experiment on this front. Our primary objectives are to successfully fire two stages and recover both successfully, rather than max out our stages or our altitude (which are other avenues in the competition to gain points). This rocket is also geared towards freshman and sophomore members, who will be able to get hands-on design experience through this build. We will continue to work on Snoopy through Mid-October 2017.
SolidWorks model of Snoopy, our two stage rocket for the University Student Rocket Competition hosted by SEDS USA
Senior Design Project - "FINesse"
FINesse, a senior design team sponsored by Rice Eclipse, has developed a system for active control of a high power rocket with actuated canard fins. The system was successfully tested in the Spring of 2017, with the results displayed at the annual Engineering Design Showcase. The FINesse team ensured that the control surfaces of the rocket was able to respond quickly to commands it receives from the microcontroller.
The team has also determined initial specifications related to the performance of the rocket. The rocket apogee increased with the application of active stabilization as compared to passive stabilization. Without this increase in performance, Rice Eclipse could not justify the cost of implementing an active stabilization system. FINesse created a detailed and lengthy documentation packet and delivered it to Eclipse at the end of the 2016-2017 year describing the design process so that this project could be replicated for future years and different projects.